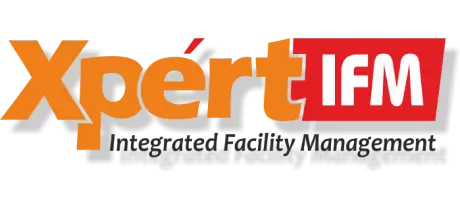
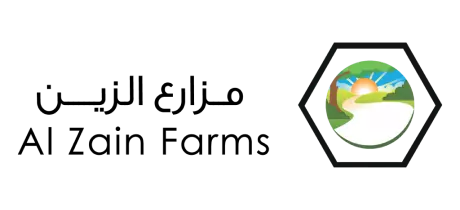
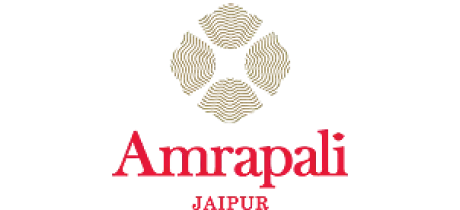
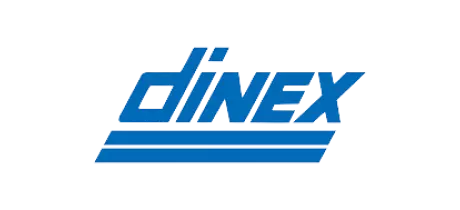
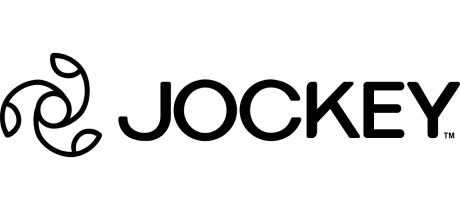
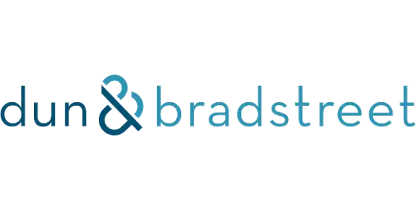
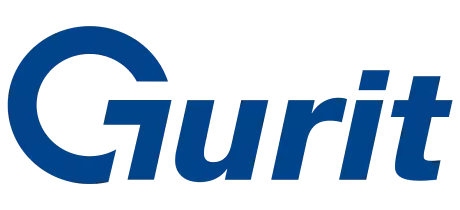
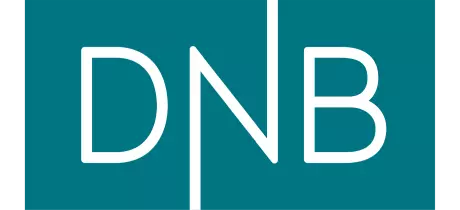
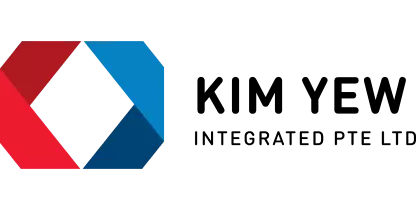
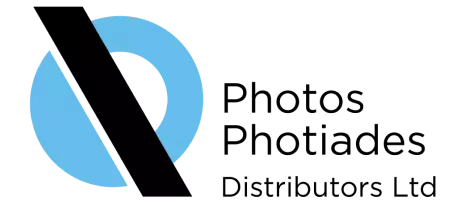
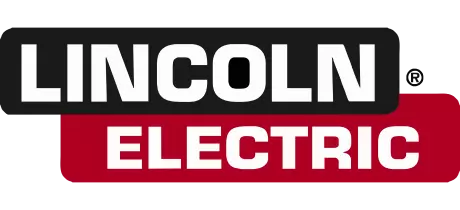
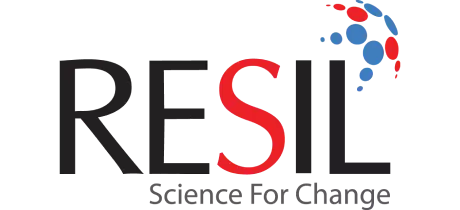
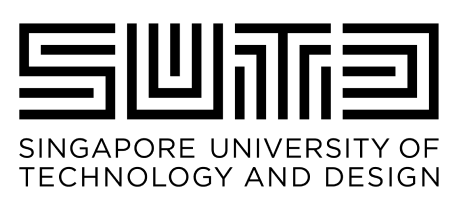
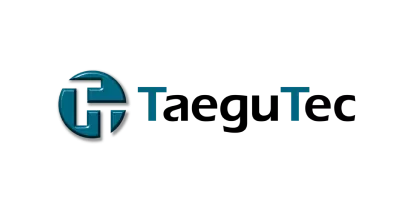
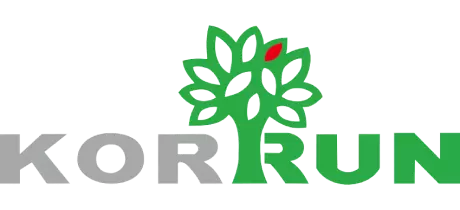
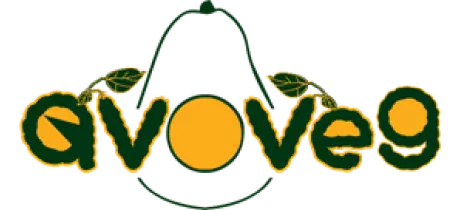
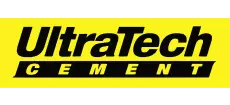
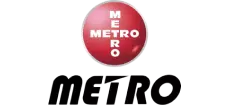
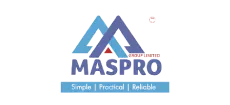
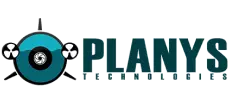
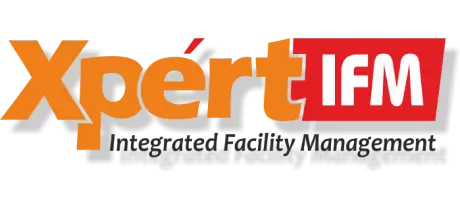
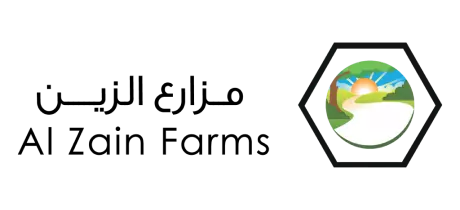
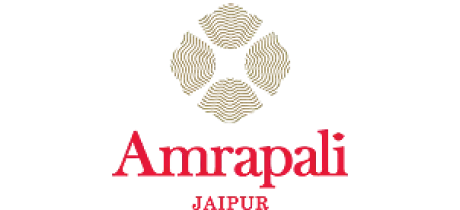
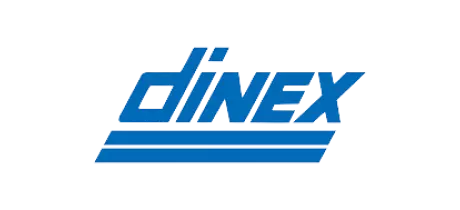
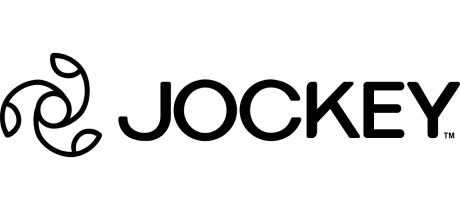
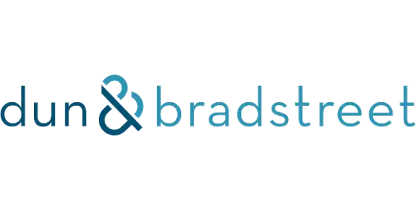
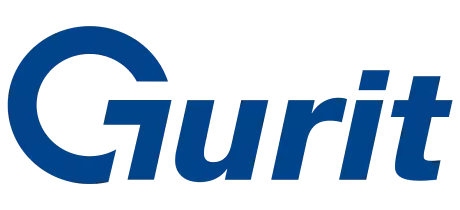
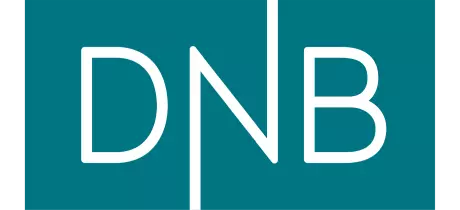
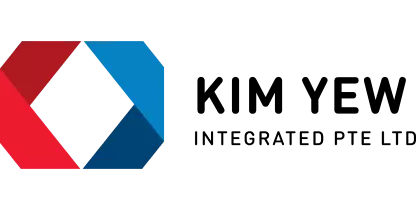
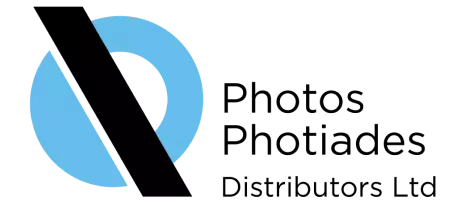
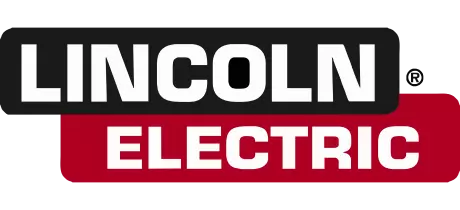
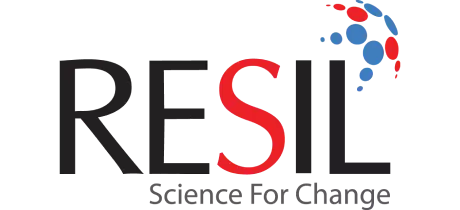
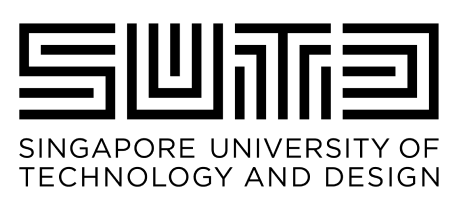
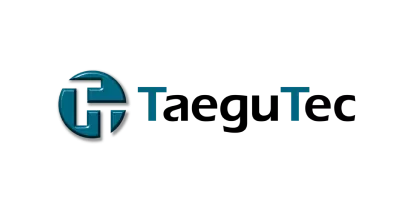
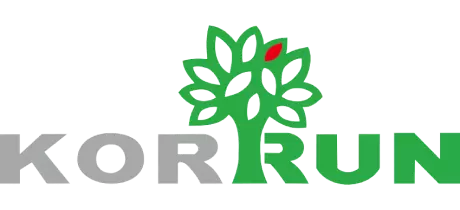
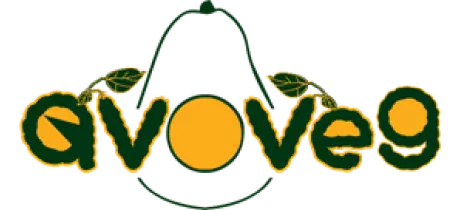
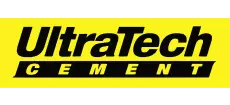
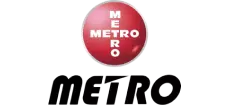
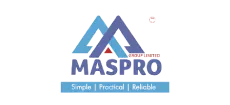
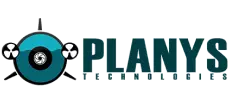
From AI-powered request generation to real-time notifications, discover how Cryotos work request system can transform your maintenance operations:
Customizable Checklist Suites: Whether you're a small business or a large enterprise, Cryotos adapts to your needs. The customizable checklist suites let your maintenance team capture and annotate photos of faulty assets or locations, with precise details like longitude, latitude, and timestamps embedded in the images. This capability ensures that every request can efficiently handle anything from simple to complex workflows.
Generative AI Assistance: Cryotos utilizes generative AI to simplify the process of creating work requests. Speak to generate concise and accurate descriptions of the issue. Additionally, AI analyzes photos of the fault, identifies problems within the annotated areas, and automatically generates detailed descriptions, enabling users to submit requests with just a few clicks.
Public Work Requests with QR Code Integration: Enhance public interaction by allowing work requests to be raised through scanning QR codes attached to specific sites, rooms, and assets. This feature includes verification via phone numbers, streamlining the process, and enhancing security and response to public maintenance needs.
Streamlined Prioritization and Detailed Descriptions: Set task priorities effectively, from urgent repairs to routine maintenance, ensuring tasks are organized and communicated clearly. This function allows for concise, transparent descriptions that facilitate quick understanding and action from the maintenance team.
Real-Time Notifications and Alerts: Keep connected with instant updates on task status changes, new requests, or critical alerts through the Cryotos system. Available on the go, this feature ensures you are always informed and prepared to tackle important tasks without delay.
Have you ever felt frustrated by the time it takes to submit a simple work request? Especially when you're not a maintenance expert and just want to report an issue quickly? We get it. The process should require minimal effort, with no need for lengthy descriptions.
To simplify this process, Cryotos work request software leverages generative AI technology. Here's how it works:
Snap a picture: Use your phone or tablet to capture an image of the issue.Let AI do the heavy lifting: Our intelligent system analyzes the image and recognizes the problem based on annotations already present in it.
Choose from smart suggestions: The AI suggests the most relevant issues, allowing users to select the appropriate one quickly.
As a result, users can raise a work request in less than 30 seconds, significantly reducing downtime and streamlining maintenance operations. This efficient method ensures that non-maintenance staff can easily report issues without disrupting their workflow, making the maintenance process as efficient as possible.
Simplify the process of creating work requests by integrating with WhatsApp, making it easier than ever for your team to initiate maintenance tasks. This approach allows team members to submit details directly through WhatsApp, streamlining the entire process.
Here's how it works: Team members select the necessary details through an interactive WhatsApp conversation. They are then prompted to upload a picture of the issue, which the system uses to generate a work request automatically.
This method simplifies and significantly speeds up the creation of work requests, enabling swift action on maintenance needs.
Instant Updates: The moment you submit a request, you'll start receiving real-time updates directly to your preferred device. Choose from mobile notifications, email alerts, or even WhatsApp messages – whichever works best for you.
Clear & Concise Information: We don't just tell you that something has changed; we explain why. If there are any delays, such as parts being unavailable or scheduling conflicts, you'll receive a clear explanation.
Stay Flexible: We understand that everyone has different communication preferences. That's why we're committed to integrating with various notification platforms to best suit your needs.
Cryotos Work Requests software leads the way in transforming maintenance management by combining high precision with exceptional efficiency. Here are the top benefits:
Streamlined Submission Process: Cryotos offers an intuitive interface that simplifies the initiation of work requests, allowing for quick and accurate submissions that efficiently capture all essential details.
Automated Workflow Integration: Cryotos reduces manual handling and accelerates the maintenance response process by automatically routing work requests into existing workflows.
Real-Time Notifications: Keep up-to-date with real-time updates delivered through various media, including email, mobile notifications, and WhatsApp. Cryotos ensures all stakeholders are promptly informed about the status of work requests and changes.
Enhanced Data Accuracy with AI: Cryotos utilizes artificial intelligence to improve the accuracy of data in work requests. It employs predictive analytics to autofill fields, significantly reducing errors and saving time.
SLA-Based Notifications: Cryotos supports adherence to service-level agreements by providing SLA-based notifications. This ensures all involved parties are aware of time-sensitive priorities and compliance requirements, helping to manage expectations and uphold service standards.
Comprehensive Dashboard: Cryotos features a robust dashboard that offers a clear overview of all maintenance activities. This dashboard allows maintenance heads to prioritize tasks based on real-time data and insights, optimizing resource allocation and maintenance planning.
A work request is an initial document or form used to describe and submit a maintenance task. Once approved by the maintenance team, it becomes a work order.
Creating a Work Request in Cryotos CMMS is a straightforward process that empowers users to report maintenance issues effortlessly. Here's a step-by-step guide:
a. Log In: Start by logging into your Cryotos CMMS account. If you don't have one, you must sign up first.
b. Access Work Requests: Navigate to the "Work Requests" section, usually found in the main menu or dashboard.
c. Submit a Request: Click the "Submit New Request" or similar button. This will open a form where you can input details about the maintenance task or issue.
d. Fill in Details: Complete the form by providing information such as the task description, location, the assets involved, and the priority level. You may also choose to attach images for better context.
e. Submit: After double-checking the information, click the "Submit" button to send the Work Request.
f. Confirmation: You will typically receive a confirmation message, and the request will be logged in the CMMS system.
g. Tracking: You can track the progress of your request through the CMMS interface. As the request's status changes, you'll receive updates and notifications.
Maintenance Work Requests and Work Orders are related but serve different purposes in the maintenance management process:
Maintenance Work Request: This is the initial step where anyone within an organization can report a maintenance issue or request maintenance work to be done. Work Requests are typically submitted by non-maintenance staff, such as employees who notice a problem. They are used to initiate the maintenance process and determine whether the issue requires action.
Work Order: A Work Order is a more detailed and formal document. Maintenance managers or supervisors typically generate it based on approved Work Requests. Work Orders contain specific instructions for maintenance technicians, including details like the scope of work, materials needed, scheduling, and cost estimates. They are used to assign and track the actual maintenance work.
In summary, Work Requests are the starting point, while Work Orders are the formalized documents that guide and track the execution of maintenance tasks.
Work Requests can vary in nature, but they generally fall into several categories:
Repair Request: These are requests to fix equipment or facilities malfunctioning or needing repair.
Maintenance Request: Maintenance tasks, such as inspections, lubrication, and cleaning, are part of routine preventive maintenance schedules.
Service Request: Requests for specific services, such as HVAC servicing, plumbing repairs, or electrical work. Equipment Request: Requests for new equipment or modifications to existing equipment.
Safety Request: Requests related to safety concerns, such as fixing hazards or ensuring compliance with safety regulations.
Renovation Request: Requests for building or facility renovations or improvements.
Each type of request serves a different purpose within the maintenance management process, helping organizations efficiently address various maintenance needs.
Work Requests play a pivotal role in enhancing maintenance efficiency in several ways:
Streamlined Reporting: Work Requests provide a centralized and standardized way for employees to report issues, reducing confusion and ensuring that all relevant information is captured.
Proactive Maintenance: Work Requests enable proactive maintenance by allowing issues to be reported as soon as they are noticed, preventing minor problems from escalating into major breakdowns.
Priority Setting: Maintenance managers can prioritize tasks based on the severity and urgency of Work Requests, ensuring that critical issues are addressed first.
Resource Allocation: With detailed information in Work Requests, maintenance teams can allocate resources more effectively, including labor, materials, and equipment.
Documentation: Work Requests are a historical record of maintenance issues, which can be valuable for analysis, compliance, and future planning.
Transparency and Communication: Work Requests facilitate clear communication between employees, maintenance teams, and management, ensuring everyone is on the same page regarding maintenance needs and progress.
Work request software streamlines the submission, tracking, and management of maintenance requests, ensuring they are addressed promptly and effectively, which enhances overall operational efficiency.
Yes, modern work request software supports mobile interfaces, allowing users to submit and manage requests directly from their smartphones or tablets.
Emergency requests are prioritized and addressed immediately due to their urgent nature, while routine requests are scheduled based on their impact on operations and available resources.
A work request usually includes details like the nature of the problem, location, urgency level, and any relevant photos or documents to clarify the issue.
Work request software provides real-time updates and tracking features, enabling users to view the current status of their requests at any time.
If there is a delay, the software will notify the requester with an explanation, such as parts availability or scheduling conflicts, ensuring transparency.
Yes, many work request systems can integrate with other maintenance and operational software for seamless data sharing and process efficiency.
While most work request software is designed to be user-friendly, basic training is recommended to ensure users can effectively utilize all features.
The software sends notifications and alerts via email, mobile, or other integrated communication platforms to inform users about updates or required actions on their requests.
I recently purchased Cryotos CMMS Software for asset management needs at my organization and after a few months of testing and monitoring, I'm incredibly pleased with the results. The software is user friendly, accessible and the design is very intuitive. It covers all the aspects of managing maintenance and repair, starting from preventive maintenance and standardizing operation cycles, to scheduling and streamlining workflows. I am highly satisfied with the performance and the range of features offered by Cryotos. Highly recommendable!
Read Review in G2Since we've started using Cryotos, our team has been able to stay on top of all the various SOPs. Checklists and safety procedures are now easily accessible to everyone, and we can quickly reference them whenever we need to. The software has definitely helped to improve our team's communication and efficiency. Plus, the fact that it's cloud-based means we can access it from anywhere, which is a big plus. It has been a great help in keeping everyone on the same page and up to date with the latest procedures.
I am using this application right now for my service team, very good, user friendly, have lot of customisation in workflow and service reports. the team supported for initial implementation, They have good support team. Myself fully recommended this application.
Read Complete Review in G2